Printing Methods 101
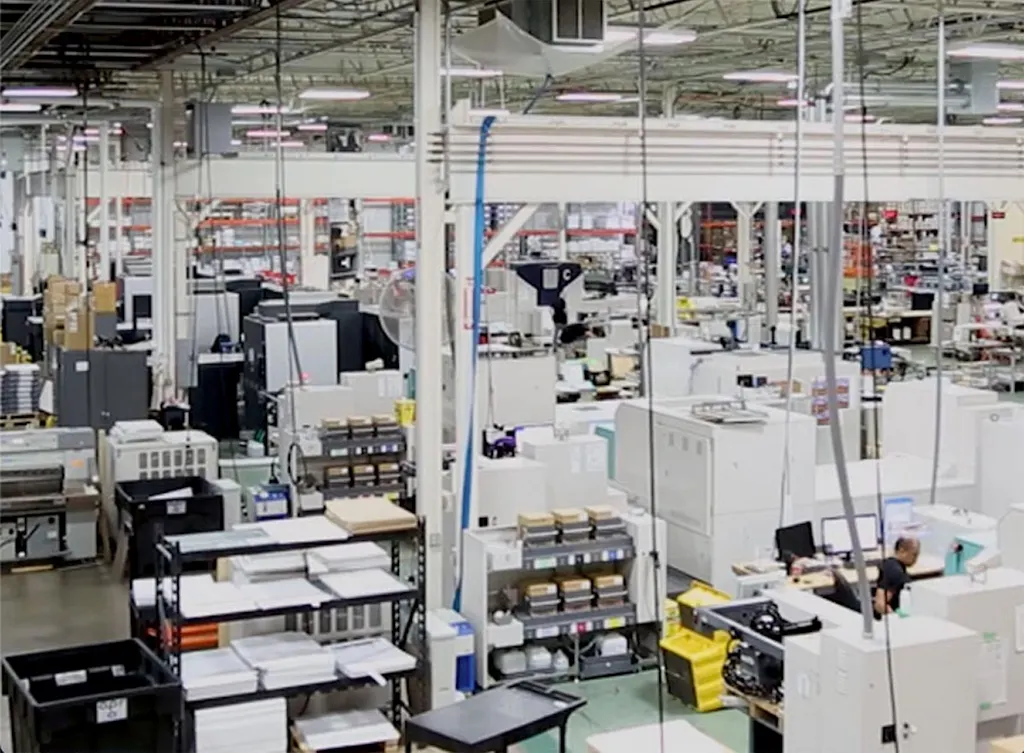
The diversity and scope of the printing industry can be pretty overwhelming if you’re just getting started as a designer or find yourself suddenly responsible for your company’s print procurement. Even a little knowledge of both historic and developing printing methods is important in order to understand the capabilities and unique aspects of each.
Learning some of these printing basics can also help you plan projects more efficiently at the creative stage and navigate obstacles you may encounter during production.
The modern online printing services industry relies heavily on new technology, process control and automation. The last 20 years has seen a dramatic shift, as digital print technologies have replaced or enhanced legacy processes. These digital solutions will continue to evolve and help drive advancements in quality, efficiency and sustainability.
As we move ahead with new tools, much of the established terminology related to traditional printing methods remains. There are also certain qualities and characteristics that may never be replaced by digital solutions. Here is a quick look at primary print methods and some examples of common uses, benefits and challenges.
Letterpress Printing Method
Letterpress is a form of relief printing, which is done by applying ink to a raised surface and then pressing paper against it to transfer the image. The earliest forms involved hand-carving wood, stone or clay one page at a time. Johannes Gutenburg revolutionized print with the invention of movable metal type in the mid-1400s.
This created the process of typesetting, where pages were built from individual characters that could be reused and set many times. This allowed for mass communication and education, as books and newspapers could be produced at much lower costs.
Letterpress was refined over the years and remained the primary commercial printing method into the 20th century.
General Uses
- Still popular for invitations, business cards and shorter runs of commercial materials.
Benefits
- Metal type and common use of heavier cotton-based paper stocks provides a natural deboss effect in image areas.
- A uniquely nostalgic and tactile experience.
Challenges
- Generally limited to shorter runs due to high costs, longer turn times related to typesetting and lack of overall capacity available.
- Only one color can be printed at a time.
- Custom images, fonts or logos can be expensive and require custom metal casting.
Gravure Printing (Intaglio)
One of the printing methods opposite of relief printing is gravure or intaglio printing. An image is etched below the surface of a metal plate or cylinder. Ink sits in the etched depressions and is transferred to the paper or substrate with pressure. Most modern applications are rotogravure, which use etched cylinders that print directly to web (roll) substrates.
General Uses
- Very high volume catalogs, magazines and Sunday newspaper inserts.
- Also common for high volume, flexible food and carton packaging applications.
- Still used as part of the currency printing process in many countries.
Benefits
- Very economical for high quantities in the tens of millions.
- Long cylinder life and consistent quality throughout length of run.
- Inline folding and finishing options available to reduce overall cycle time.
Challenges
- Very high cost associated with cylinder etching and set-up.
- Traditional process is static print only, no variable data or personalization.
- Minimum quantities generally in the hundreds of thousands of pieces.
Screen Printing (Silk Screen or Serigraphy)
Screen printing is commonly referred to as silk screen printing, as the process originated in China using silk mesh. During this process, ink is forced through a fine mesh screen with a rubber squeegee. Non-image areas are blocked out with a stencil material so ink only passes through open areas to the substrate underneath.
Although it’s still common to do small projects manually, there are automated solutions for producing higher volumes.
General Uses
- Apparel, promotional items, circuit boards, signage and other display-related products.
Benefits
- Very versatile in terms of the variety of substrates (materials), specially formulated inks, custom Pantone spot colors and coatings for custom applications.
- Provides durable and heavy ink coverage.
- Cost effective for short to long runs.
- May also be applied to dimensional objects like cups or promotional items.
Challenges
- Best suited to static images and difficult to manage variable data or personalized applications.
- Limited ability to print fine detail or small fonts.
Flexographic Printing Method
This is another, more flexible form of relief printing, in which ink is applied to a raised surface and transferred directly to the substrate. The flexographic printing process, or “flexo” for short, uses flexible rubber-based plates wrapped around a cylinder to print on primarily roll (web)-based materials.
General Uses
- Used extensively in label and packaging industries.
- Common press configurations allow for inline laminating/gluing of multiple layers of materials, coatings, adhesives, embellishments and die cutting.
- Also used in high-volume envelope and carton printing applications.
Benefits
- Very economical for high volumes.
- Ability to print on extremely thin plastic films.
- Allows for very complex inline laminating, coating and die-cutting applications.
- Can print Pantone spot colors.
Challenges
- Can have high set-up costs due to custom dies and complex make-ready process.
- Limited print quality for 4/c photographic images, as compared to other processes.
- Difficult to maintain fine line art and fonts.
- Traditional flexo process is static print only, with no variable data or personalization.
Offset Printing (Lithography)
Offset, or lithography, is the most common commercial print process and is used in two configurations: sheet fed and roll (web)-based printing.
Printing is done with a flat metal plate that transfers ink from the image areas to a rubber-coated blanket cylinder, which then “offsets” the ink to your paper or substrate material.
Sheet fed presses range from small presses running items like 3.25” x 5” envelopes up to very large format machines running 81” x 59” board stock. Web presses can range from paper roll widths of 12” up to 112”, with the largest presses able to print 96 standard catalog or magazine pages at a time.
General Uses
- Most common type of printing for magazines, catalogs, collateral, direct mail components, calendars and other paper-based materials.
- Also used for other substrates like rigid plastics and corrugate.
Benefits
- Very economical for medium to high volumes.
- High quality and durable inks with inline coating options.
- Ability to print Pantone spot colors.
- Large web offset presses print both sides of the paper at the same time.
- Typically have inline drying and options for coating, folding and finishing operations that reduce overall schedule time on high volumes.
Challenges
- Traditional process is static print only, with no variable data or personalization.
- Costs associated with plates, press make-ready and spoilage are cost-prohibitive for shorter runs or projects with many versions.
- Most sheet-fed options require drying time between sides and/or after printing, which extends schedule.
Electrostatic or Electrophotographic Printing (Xerography)
As printing methods go, you might be more familiar with this one – it’s the technology used by your toner-based office printers and copiers. It is also used in larger production machines that use either dry toner or variations of liquid-based toners. LED lights or lasers place a static charge on an imaging drum, which attracts the toner to the drum with the opposite charge.
The charged toner is then transferred either directly to the print substrate or via a transfer roller similar to a blanket roller in offset printing. The substrate passes through a heating unit that melts and fuses the toner to the surface.
General Uses
- Most common type of printing for short run magazines, catalogs, collateral, postcards, self mailers, calendars, stickers and other paper-based materials.
Benefits
- No plate or make-ready costs and very little paper waste.
- Great for producing full-variable content, highly-versioned content and personalized pieces like direct mail.
- Versatile substrates including paper and synthetics.
- Great alternative to short run offset printing.
Challenges
- Cost-prohibitive for medium to high volume projects.
- Wide variety of equipment manufacturers results in inconsistent quality between different printers.
- Toner tends to scratch more easily than traditional inks, making it important to flood coat pieces to increase durability.
Inkjet Printing Method
Inkjet is the fastest growing and developing technology in the printing industry, as we move into the 2020s. Behind the scenes, there are a couple of different technical processes, but for practical purposes, it involves hundreds or thousands of individual nozzles spraying tiny droplets of ink on the surface of the substrate for each color.
This is one of the printing methods being used in a diverse range of digital presses that’s taking the place of some legacy print processes mentioned above. Here are some of the configurations:
Cut Sheet Presses
As the name implies, these print directly to sheet stock ranging from letter size (8.5” x 11”) up to B2 size (20” x 29”). Most use water-based ink and print to paper, but there are some with UV cured inks that can print to a wide range of synthetic stocks, as well as some emerging options for larger 28” x 40” sheets.
These are replacing short run offset printers, with speeds ranging from 1,000 to 4,000 sheets per hour.
Production Inkjet
These web (roll)-fed machines run at high speeds from 300 to 1,000 feet per minute and print on roll widths from 8” up to over 40”. Heavily used in transactional/direct mail printing, as well as the the book market, these can print 30,000 to 50,000 letter-size pages per hour.
They are replacing web offset and flexo printing, with rapid growth in the label and packaging sector as well.
Large Format Flatbed Printers
These are designed to print rigid materials ranging from paper, plastics (PVC, styrene, acrylic, PETG, etc.), metals and wood to nearly any other material. Many machines are 60” x 120” or even larger, use UV-cured inks and can print on materials several inches thick with speeds typically 50 to 300 beds (sides of a sheet) per hour.
This is one of the printing methods replacing screen printing and large format offset sheet-fed printing.
Large Format Continuous Printers
These are used for flexible materials including things like vinyl banners, window clings, clear films, wall graphics, floor graphics, photo paper, etc. These machines can be up to 20 feet wide and use water-based, latex or UV-cured inks with speeds generally slower than flatbed printers.
Like large format flatbed printers, these are also replacing screen printing and large format offset sheet-fed printers.
Dye Sublimation Printers
Most dye sublimation is done in a two-step process that begins with inkjet printing to a paper-based transfer substrate in reverse. The inks used chemically bond with any surface that is treated with a polyester-based coating. Applying heat and pressure causes the ink to vaporize from the transfer paper and bond to the final object.
The primary use is for fabrics in the apparel industry, backdrops and soft signage and interior decorating. You can also sublimate to rigid materials like aluminum, MDF board and 3D objects like high-end aluminum photo displays and promotional items.
These printers are replacing screen printing.
Direct-to-Object Printers
Of all the printing methods, inkjet is emerging as the go-to technology to print to 3D objects. Anything from water bottles to golf balls can be personalized quickly and easily in small or large batches.
There are also new printers that can handle large scale direct-to-wall murals and dimensional print for Braille and texture. These printers are replacing screen printing.
Benefits
- Diversity of specialized ink types allows it to be tailored to a wide variety of print applications and products.
- Full variable content and personalization capabilities with very little material waste.
- Imaging heads do not make contact with product, allowing for flexibility with thicker substrates and dimensional object printing.
- Can be easily integrated with more traditional print and finishing processes to increase production efficiency.
Challenges
- Speed in relation to image quality for high volume commercial and direct mail printing.
- There is a trade-off of image quality for increased speed.
- High-speed production inkjet printing used for long run direct mail, books and statement printing is good quality and acceptable in some of these applications.
- For great or exceptional image quality on coated papers, there is a substantial gap compared to offset printing.
Hybrid Printing
Think of this as the best of both worlds: integrating new digital technology inline with traditional printing methods like offset, flexography or rotogravure.
High-volume direct mail printers use inline web presses, which allow them to print static copy and images with traditional offset units, add variable copy with inkjet imaging heads, fold, glue and die cuts and affix items like cards or small inserts all on one continuous production line.
You can go from a blank roll of paper to a complex, personalized mailer in a matter of seconds, as it produces hundreds of thousands of pieces per hour.
This same inline concept of adding variable inkjet to existing press lines is also being used with flexography for labels and flexible packaging, as well as rotogravure for carton printing.
Parting Thoughts
Printing methods will continue to evolve, as the industry becomes more reliant on online printing and digital processes in the 2020s. The emergence and growth of digital and online printers over the last two decades has coincided with huge leaps in automation, process control and speed for offset, flexo, rotogravure and screen printing.
There are still considerable advantages in efficiency, quality and cost that will keep the traditional processes relevant for certain products and use cases well into the future.