Ink Technology: Aqueous, Latex, UV Ink and More
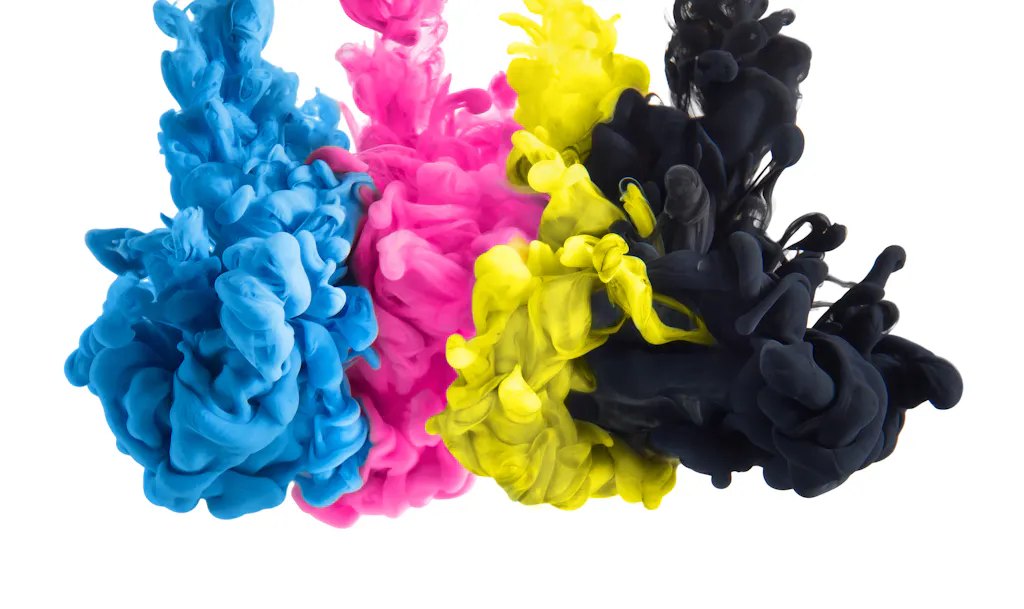
Smartpress’ online printing services include an impressive large format digital printer fleet consisting of four different ink technologies: aqueous, UV ink, latex and disperse dye-sublimation.
Each ink set has its own capabilities, limitations and benefits. For example, we aren’t able to print aqueous ink or latex ink onto a rigid substrate but we can print UV ink on just about anything that we can hold down with a vacuum (non-porous medias).
And while all of them contain various amounts of water, they use different methods of curing or drying and contain small amounts of stabilizing compounds such as antimicrobials, anticoagulants, etc.
Aqueous-Pigment Ink
Online printing with our aqueous-pigment ink printers means you’re getting the highest quality prints in our fleet. They’re the closest to photographic-level quality you can get. We use them to print on several different medias, including photo-satin paper, pearlescent photo paper, matte coated paper and backlit film.
Containing mostly water and pigment or dye, there is no additional curing process other than air-drying that is sometimes assisted with heat. No heaters or lamps are used to dry aqueous ink, so the print speed is slower than latex and dramatically slower than UV-curable or dye-sublimation printing.
It is recommended to laminate aqueous prints by encapsulating them with thermal or pressure-sensitive adhesive laminates.
Pros
- Superior photographic quality due to very small dot size and high resolution printheads
- Large color gamut
- Ink lay-down is smooth and thin
- Odorless
- Incredibly environmentally-friendly, no volatile organic compounds (VOC)
- Minimal metamerism
- Good indoor lightfastness, even better when laminated
Cons
- Slow print speeds
- Prints need protection from liquids (lamination strongly suggested)
- Poor outdoor longevity and lightfastness
- Limited printable substrates
- Expensive ink costs
- Requires more expensive aqueous receptive coated medias
Latex Ink
Our latex ink printers print in high quality and medium-to-high speed. Latex ink offers a unique look combined with very strong adhesion to the print media resulting in super-tough graphics. Latex ink is a mixture of latex, water and pigment.
It is cured by infra-red heat and hot air which evaporates the water and melts the latex and pigment, bonding with the print media. There are pre, platen and post heaters that aid in this process.
There is an additional channel that fires an optimizer liquid which lays down between the ink and substrate to help with adhesion and scratch-resistance. It is unique in that it only lays down where ink is being fired and it varies in volume, relative to the amount of ink being printed.
Our latex printers are capable of printing on a wide array of rolled print media. Some examples are vinyl banners, pressure-sensitive adhesive (PSA) vinyls, canvas, some fabrics and a variety of reflective and metallic films.
Depending on the end use, latex prints may or may not require lamination. Some PSA vinyl products require lamination as a condition of their warranty.
Pros
- Inks are GREENGUARD and ECOLOGO certified
- Ink lay-down is smooth and thin
- Inks are so translucent that the printed result takes on the property of the substrate (i.e., a gloss media will produce a glossy print, a metallic media will produce an equally-reflective metallic looking print, etc.)
- Latex ink is very conformable/flexible and will not crack when bent or stretched
- Great for any type of vinyl printing such as car, bus and truck wraps or simply a removable wall poster
- Banners, paper prints, canvas, backlit and other print projects require no lamination to protect the final product
- Ink is waterproof and has a great outdoor lightfastness and resilience
Cons
- Slower than UV ink printing due to the heat curing process
- Heat curing can make for difficult printing on heat sensitive materials
- Due to the translucency of the ink, more ink is required to achieve a given color, making ink usage costs higher than a UV-curable ink
- Cannot print on as many substrates as a UV-curable ink
UV-Curable Ink
Our UV-curable ink printers have the highest speed. Because the ultraviolet light cures ink almost instantly, it allows for printing at much higher speeds. The UV lamps cure the ink which dries on top of the print substrate, adhering to the board’s surface energy or dyne level.
This enables UV ink to print on a broad array of both rigid and rolled print medias – vinyl, wood, metal, plastic-based material, cardstock, foam boards and corrugated plastics and papers.
When considering a rolled material, UV ink can print on nearly any substrate including some fabric materials. UV-curable inkjet printers also offer white ink. This allows us to print to clear, metallic and colored medias while still achieving a pleasing color, like white substrate prints with colored backs and edges or translucent and special effect prints.
UV inks consist of water, pigment and a photo-initiator to enable curing at high speeds with UV radiation generated by mercury vapor arc lamps and/or LED lamps.
Pros
- Highest speed print technology
- Color gamut can be improved with additional extended gamut ink channels
- UV ink can produce glossy or matte prints without lamination
- Can achieve spot gloss
- Multiple pass printing to achieve textured prints
- Most have white ink printing capability for special effect prints
- Prints to almost anything – rigid, flexible or roll media
- Inkset includes CMYK plus orange, white, light magenta and light cyan
- Orange boosts gamut while the light inks achieve smoothness in highlights to midtones
- Durable for at least 18 months in most outdoor conditions
- Economical ink usage and cost
Cons
- Higher purchase cost for printer
- Inks can be too brittle to bend or stretch
- Ink lay-down has some texture
- CMYK-only printers’ color gamut is generally smaller than latex ink or aqueous
- Not as good as latex for vehicle wraps that require flexibility or adhesion to complex curves
- Laminating can be difficult due to raised texture of the printed ink
Disperse Dye-Sublimation Ink
This ink printing technology is the most difficult and interesting of all. It involves first printing to a transfer paper with a mirrored image and then transferring that print to another polymer-based or coated substrate for embedding into the polyester or polymer coating.
It’s mostly used for printing to polyester-based fabric for trade show displays, table throws or fastened to free-standing or wall-mounted frame systems. It’s also used to create a high-end photographic look on metals or other rigid substrates with a polymer coating.
When printed to transfer paper, dye-sublimation ink is subjected to heat, time and pressure to turn it into a gaseous form that penetrates into the polyester fabric fibers or a polymer coating. The ink does not sit on the surface but is absorbed into the polymer/polyester. Therefore, when done properly, the print is waterproof and scratch-proof.
It is the best print method for achieving vibrantly-colored images. If you’re using a high-resolution printer, the result is photographic quality, since you cannot see any dot structure due to the sublimation process.
The devices that apply the heat and pressure come in various forms. For large format printing, they are in a calendared roll-fed device, like a laminator, or a flatbed pressing type of device, which is required for rigid substrates but can also transfer fabrics that fit the bed area.
A typical transfer time and temperature is around 400 degrees Fahrenheit for approximately 45 seconds on fabrics. This can vary widely with rigid substrates, up to eight or nine minutes at 325 degrees Fahrenheit.
A very popular form of display for the retail industry is a Silicone Edge Graphic or SEG. This consists of an extruded aluminum frame of various depths and shapes that has a groove around the front perimeter and is usually attached to a wall.
The fabric edges have a flexible strip of silicone that fits into the frame’s groove and provides a clean, easy-to-install, interchangeable graphic.
Pros
- Best method for printing to fabric
- Fabric prints are lighter and easier to ship, handle and install
- Easier to replace fabric graphics in SEG frames
- More environmentally-friendly than UV printing
- Lowest ink usage and cost
Cons
- After printing, it requires a secondary step to finalize the image (sublimation)
- Initial cost is higher due to the requirement for an additional device (sublimation unit)